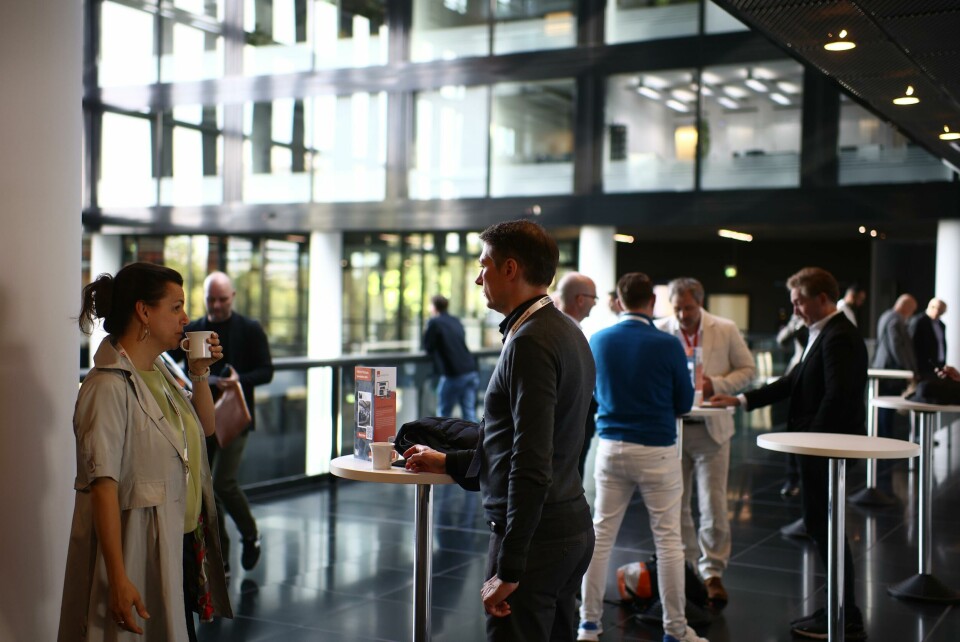
Live blog: Design4Production
Get all the highlights as they happen at Design4Production in Munich
Good morning from Munich, where Design4Production has kicked off. We will be covering all the sessions of the day here – so check back for updates as they come.
Getting things started (and strolling out to ‘She’s Electric’ by Oasis) were CDN editor James McLachlan, Automobil Producktion editor-in-chief Pascal Nagel and Ultima Media’s chief content officer Christopher Ludwig. The aim, they explained, is to explore how historically separate divisions in design and engineering can – and are – working more closely today, helping to produce better products with greater ease.
9:00: The opening session brought two big names in design to the floor, with Tata’s Martin Uhlarik and Changan’s Klaus Zyciora joining McLachlan on stage to discuss the theme of “breaking down silos.” A key takeaway is that communication is vital – helping each side to understand the shared goals on the table.
Uhlarik was keen to underline how Tata is developing not just physical products – vehicles – but exeriences, which can be a challenging conversation to have with an engineering department. “We’ve always been seen as a little bit weird as a department, but when you’re talking about feelings, ultimately [engineers] use a vehicle as well,” says Uhlarik. “You have to be a storyteller and explain your point of view and what the customer is trying to achieve. The best way is to experience that together, whether that is going on test drives, working on model bucks or whatever. So in many ways, the role of a designer is to convince people that there is another way to look at things.”
I want engineers to want beautiful cars and designers to want functional cars
Zyciora joined the conversation by touching on the differences between a European OEM like Volkswagen Group, where he was previously head of design, and at his new company, the Chinese giant Changan. “There is quite a difference,” Zyciora explains. (Editor’s note: watch our separate interview with Klaus here)
“VW has a huge legacy and a very traditional type of role management: the designers make the things beautiful, execute the shapes, and of course influence the architecture and experience design,” Zyciora continues. “In China, things are pretty different, it is very co-creational and design has a much bigger stake in the game, leading the product development quite a bit. But again, it is ultimately very customer-oriented. You’re in constant exchange with consumer groups, and the old game where engineers tell designers something looks crap and doesn’t work isn’t really happening in China.”
At this point, it was time to guage the sentiment in the room which seemed to be evenly split between designers and engineers. One audience member from Callum design noted: “It is fantastic to hear about the engineering and design collaoration. I want engineers to want beautiful cars and designers to want functional cars and meet in the middle. It’s very encouraging to hear that.”
“Today It’s more like brothers in arms working together to create a leading product,” added Zyciora. “You better get used to your neighbours – your’re a team.”
9:45: The next session was chaired by Nagel and brought together Audi’s Jan Pflüger and Daniele Sirigatti, who shared how the brand’s AI-aided design platform has been revolutionising the design process.
Taking the example of a wheel design, the pair explained that GenAI had initially been used as part of a very small trial, but today has become an everyday tool. “You can mix and match designs, and we saw that designers found this interaction very interesting,” said Sirigatti. “The aim of the platform is to boost creativity in the early stages of design, iterate more quickly and reduce costs in the design process.”
But what does all this mean in terms of the engineering department? For example, entering package data, dimension concept to use hte tool to solve engineering challenges? Sirigatti was a studio engineer prior to his current job at Audi, so was well placed to comment. “We have of course the plan of starting to do that, but it is very early stages. We are expanding it to where it could be used across all departments, including engineering.”
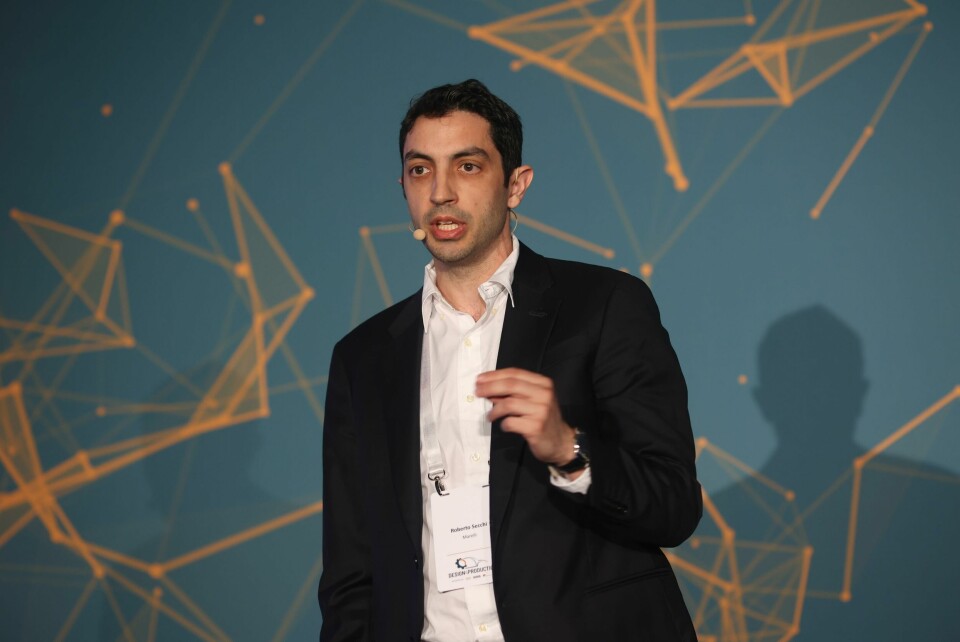
10:30: Marelli’s Roberto Secchi was up next to share a supplier’s perspective on design-led innovation. The general idea is use Digital Twin and LightStudio tools to help designers and engineers transition to software-defined vehicle architectures. In simple terms, these tools utilise cloud computing to reduce development time.
The larger the company, the more silos there will be to break down
In Marelli’s experience so far, Digital Twins of a vehicle’s full E/E architecture have allowed complex development processes to be simulated, leading to a 70% reduction in development time and 30% reduction in prototyping costs. Virtual replicas like these can cover both the cockpit and body architectures, says Secchi. And importantly, it has improved inter-team collaboration.
11:15: From digital design to very much physical. Hyundai’s Emilie Grimm kicked off the post-networking session by digging into the world of CMF, which as she emphasised, is about as collaborative as it gets: working with suppliers, purchasing and manufacturing to ensure target are met in production, recycling, and reuse.
“When we develop a material, we have a strong collaboration with engineering but also our suppliers,” said Grimm. “In general, to go more towards circularity we need to have an overall stronger collaboration within design itself. But we have around 15 innovative materials we are trialling already, so we are at a good start.”
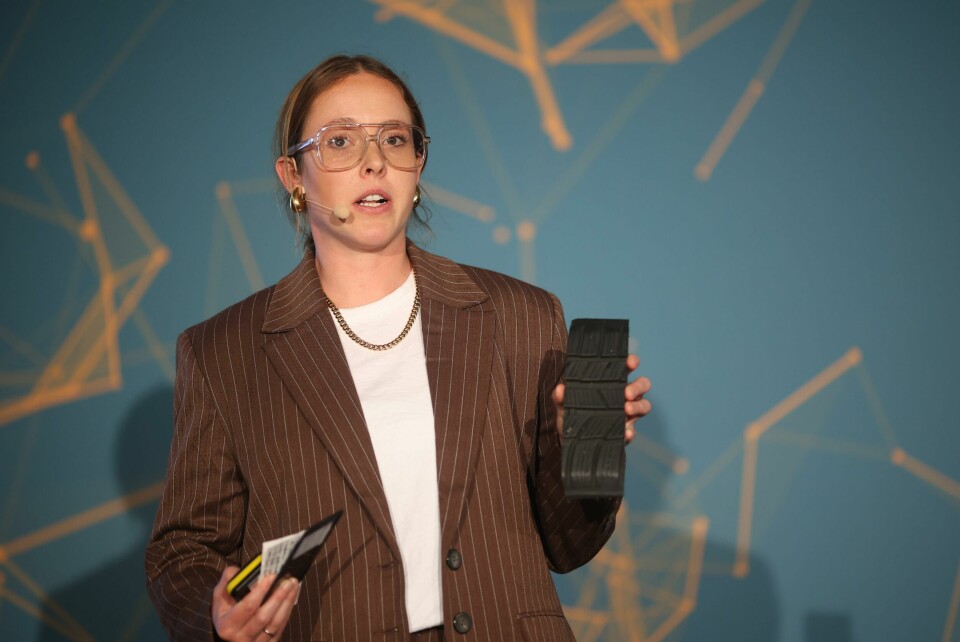
One of the discussions around sustainability is the idea of materials that last. With that comes natural side effects, such as wear and tear or ‘patina’, which in other industries is desired but not always in automotive – particularly for customers that are paying a premium. One of the challenges will be to convince not only customers but also internal divisions that this is acceptable – although there cannot be any compromise in terms of performance. “Especially from the engineering side, there would be concerns around lowering the specifications they are working to…That is quite a challenging thing to do in a big company.”
11:30: Joining Emilie on stage to discuss holistic design and eco-friendly vehicles were several other experts: David Mason from Nissan, Amko Leenarts from Ford and Jesse Paegle from ArcelorMittal.
Mason jumped in to follow up on Grimm’s point around materials that last and the challenges that presents. “As we put more recycled and natural content into plastics, there is sometimes a degradation in durability performance, so how does that work with internal policies for parts specificaiton, and what is the customer willing to compromise on?” Mason said. ”I can tell you that comfort is not one of those things, from our research.”
Designers love to make beautiful things. But does it have to be with more parts, more chrome, more lacquer?
Moderating the session was CDN’s editor James McLachlan, who posed the question: is the automotive industry doing enough as a whole – design, engineering and all of the above – to pursue sustainable vehicles? “We have maybe had some doubts as it simply costs a lot of money, so the business case behind it is a little challenging,” noted Ford’s Leenarts. ”Are we late? Perhaps – but it’s really good that we’re here. The more efforts we make, the better it is.”
Leenarts raised the topic of parts reduction, which plays into the work of both design and engineering departments, who – in most cases – will need to work together to find clever solutions to consolidate individual components while still meeting targets for appearance and function. “Designers love to make beautiful things. But does it have to be with more parts, more chrome, more lacquer? So I often ask my teams, what if we take it away? What is left? So there is a sense of purity to the design.”
Speaking on behalf of the steel industry, Paegle agreed that “the less material you use, the greener you will be. It is not rocket science. But going into this modularity, simplification, parts consolidation, by using steel you can give a good weight saving and remain competitive.”
But it is not only about what goes into the vehicle. It is about how they are integrated. From Nissan, the subject of design for disassembly was one that caught David Mason’s attention.
“When you set metrics as targets at the start of a project you have a greater chance of success,” Mason said. “It is a super complex topic that has to be approached collaboratively. Once those metrics are clear and everyone understands the ambition of the company, you can understand how a particular type of technnology might enhance the simplifciation process and whether you are making the right decision for the product.”
By speaking directly with manufacturing, designers can be more responsible with what decisions are made
Ford’s Leenarts agreed, particularly on the issue of collaboration. “I’ve never had more conversations with engineering than I am now,” he explained. “We always had good conversastions with engineers, but now I am also speaking directly with manufacturing to get to the bottom of what is possible, meaning we can be more responsible with what decisions are being made.”
12:20: Time for more insight from a supplier, this time, Valeo. Markus Hein was on hand to discuss simplified production and development cycles across both Tier 1s and OEMs. One of the more technical presentations that will no doubt be particularly useful for AMS and Automobil Producktion readers, one of the key takeaways was that industrial engineers should have an early involvement in the product development process.
In fact, engineers should be brought in as early as possible. By doing so, recommendations can be made in terms of simplifying production, such as: ensuring Tier 1 suppliers and the OEM are on the same page; advising limitations or boundaries to product design with the goal of streamlining production equiment needed; and standardising the kind of data being recorded across stakeholders in the development process.
“The larger the company, the more silos there will be to break down,” he added. “That’s why we are encouraging this collaborative approach.” Hein will no doubt be swarmed by eager audience members during the lunchtime break that follows this.
We will be back shortly with coverage of the afternoon sessions.
14:00: Welcome back. CDN’s senior content producer Ahmo Saric has kicked things off with our next session, joined by Hyundai’s Armand Nowak and Julius Schlecht of studiokurbos. The focus for this one is on building agile and collaborative design teams.
Perhaps equally relevant to designers, engineers and anyone else involved in a broader organisation these days, the discussion touched on the mix of virtual and physical processes i.e. in the office or at home. Schlecht recalls one scenario where he had worked with two designers exclusively online, meeting only by chance in the elevator. “This is not the ideal set up,” he said. ”But if you have 40 people in the office sitting in a teams call, this is also not ideal. I think there needs to be a balance.”
I always tell my designers not to use design vocabulary… When an engineer hears ‘volumes’ they are thinking of decibels and litres
Nowak noted that communication between different teams is also key to ensuring a collaborative team dynamic. This somehow feels both obvious and underdiscussed at once, because of course communication is important. But Nowak raises the point that different teams do not necessarily have the same mindset, personality or – to be frank – understanding of what each team does.
“We all speak English, but you can sometimes feel there are different worlds or midnsets. You have engineering that is talking about numbers, details; you have marketing that is also talking about numbers; and you have design that is more about the emotion,” observes Nowak. ”Everyone speaks English, but it is sometimes hard to have that shared understanding. Everyone needs to understand what makes each other tick. I hate it when people say “oh, they don’t get it.” We need to speak each others’ language to make sure we are aligned.”
Schlecht agreed, adding: “I always tell my designers not to use design vocabulary. We like to talk about volumes, for example, and then they go on and talk about sculpture. After 15 seconds, they have already lost their audience because when an engineer thinks about volumes they are thinking of decibels and litres. It’s about getting to the point.”
14:30: From discussing what is possible, to what is actually happening. Callum’s Adam Donfrancesco and James Horne of Motability Operations joined Ultima’s Christopher Ludwig on stage to discuss the wheelchair-accessible vehicle they have been working on. The details of that project can be found in the link, but with the theme of the event in mind, engineering director Donfrancesco highlighted what will need to happen to make that concept production-ready (as planned). “To be honest, it is mainly around the integration of the battery, which does bring some fun complexities,” he said.
Donfrancesco added that, as a team, “we want our engineers to think more like designers, and our designers to think more like engineers. It makes it easier for them to work hand in hand to address those problems.” Certainly one of the more raucous rounds of applause for the team at Callum in partnership with Motability.
As a studio engineer, this is my task: to make design ambitions real
15:30: Following a short coffee break, Hyundai’s Sven Wittke and Italdesign’s Joaquin Garcia took to the stage. The topic at hand was how to realise design ambitions; in other words, how design and engineering can work together to make a concept a living, breathing thing. As a studio engineer, this is right in Wittke’s wheelhouse.
“Imagine we are in a recording studio,” said Wittke (with impressive gravitas, we might add.) “The artist has a song – a complete album – in their mind. On the other side on a huge keyboard is the engineer, who has to understand their vision and ambition. How should it sound? How can we make it real? This is my task: to make design ambitions real.”
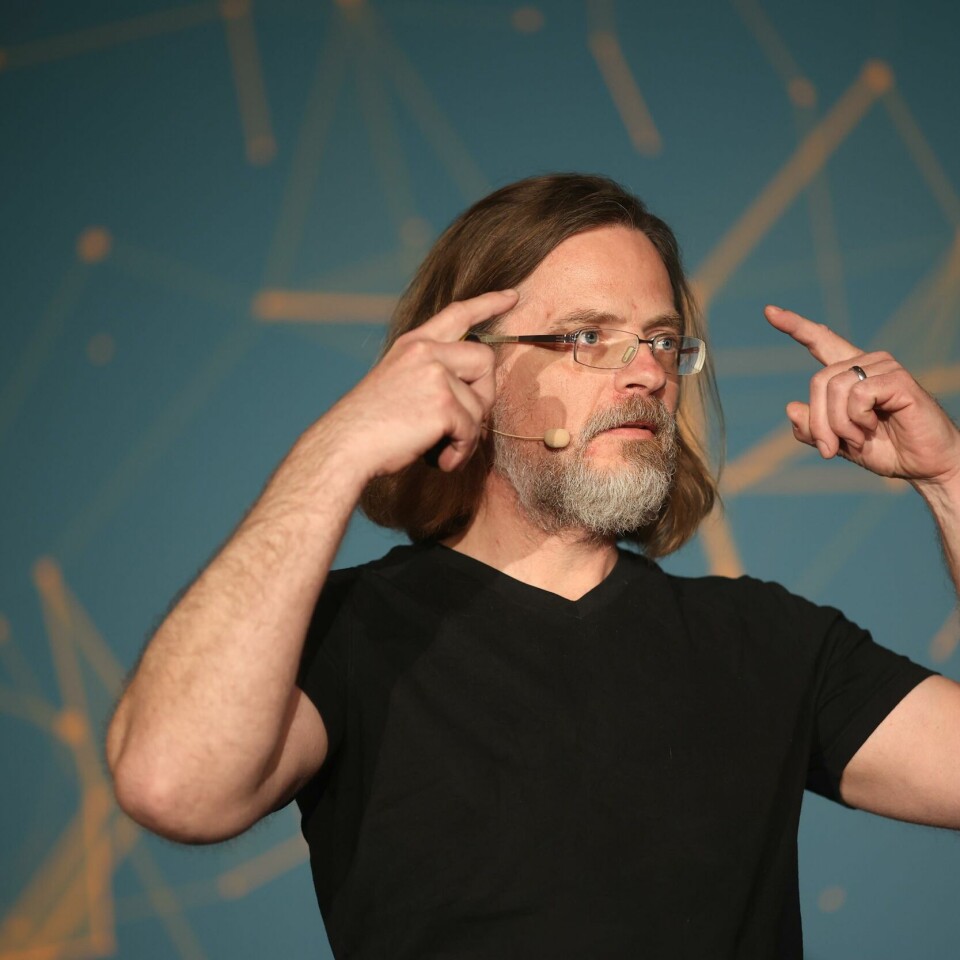
Joaquin Garcia, who has been fairly busy on the events circuit of late, was up next. The head of design at Italdesign was perhaps in a favourable position, able to reflect on some of the various themes raised during the day. One trend that caught his eye was parts consolidation and design for disassembly, which as it happens was a consideration for the company’s latest concept, the Quintessenza.
“We cooperated with a British company to integrate haptic functions within the material so you don’t have any switches,” he said. “It’s a good improvement in terms of saving cost, time and also the discarding of parts: if you have fewer parts, it is easier to recycle and dismantle the vehicle. This was an interesting path to follow for us.” Further emphasising that Garcia had been listening intently was his closing remark: “I think that designing things beautifully in a way that they last longer is the right approach.”
16:15: And so to the final session of the day. The discussion focussed on leadership, which felt quite a fitting way to wrap things up. “I’m neither a designer nor an engineer, so hopefully I can bring an outside perspective,” noted Daniel Kichert, currently the CEO of his own company Noyo but perhaps better known for founding Byton.
I encourage my colleagues to reach out, ask questions, and ask for support… That really fosters collaboration
Joining Kichert and moderator, CDN’s James McLachlan, was Gustavo Guerra – a former design director who has made the shift into product planning. Another keen listener, he addressed a recurring thread throughout the day: breaking down silos. “The culture we have in the Volvo Group is naturally very collaborative, and I don’t think anyone consciously builds silos for their own expertise or for their own sake,”said Guerra.
“I would hazard it is more down to the complexity of a particular task or the sheer size of an organisation,” Guerra continued. “If you don’t know who to ask, it is easier to just get going and do things yourself, and that’s what leads to the silo. It’s simple but I encourage my colleagues to reach out, ask questions, and look at the organisational chart to avoid that. You can ask for support, and that really fosters collaboration.”
17:00: Time to wrap up with the help of our moderators. For Automobil Producktion editor-in-chief Pascal Nagel, there was a clear willingness to break down those walls or ‘silos’; it’s more than just a catchy phrase, in his words.
For Christopher Ludwig, chief content officer at Ultima Media, it was the emphasis on cutting development times that really resonated, particularly in China where consumer trends are pushing designers to have a greater influence right through to the factory floor. For CDN’s James McLachlan, it was a line from Hyundai’s Sven Wittke – “data is stupid” – that stuck with him. “It shows that we as humans get to decide what is useful and acknowledge when to use it.”
Did you join us at Design4Production? Share you feedback with us, either via our social channels or with our respective editors. Until next time, folks.