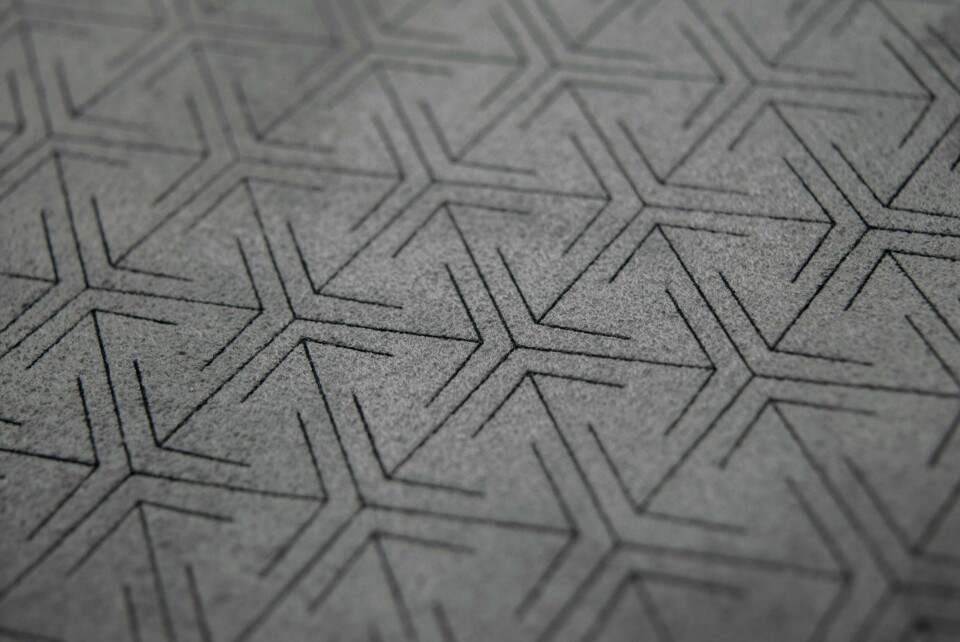
Knitting the future: Shawmut creates innovative, recyclable suede alternative
PARTNER CONTENT
This content was paid for by Shawmut and produced in partnership with Car Design News
Shawmut addresses two key drawbacks of traditional urethane-infused non-woven suedes – sustainability and ease of use – through Neoluxe
There is no shortage of materials suppliers in luxury automotive interiors, so a new brand may not be surprising. But what about one backed by an established player with a groundbreaking solution?
Enter Neoluxe, a knitted suede fabric offering notable sustainability benefits and superior functionality at a competitive price. It provides better moulding, seat wrapping and trimming, all while maintaining a soft texture and vibrant colours. After extensive testing, two premium OEMs have already adopted the material for seating, door inserts, lower IP parts and overhead applications.
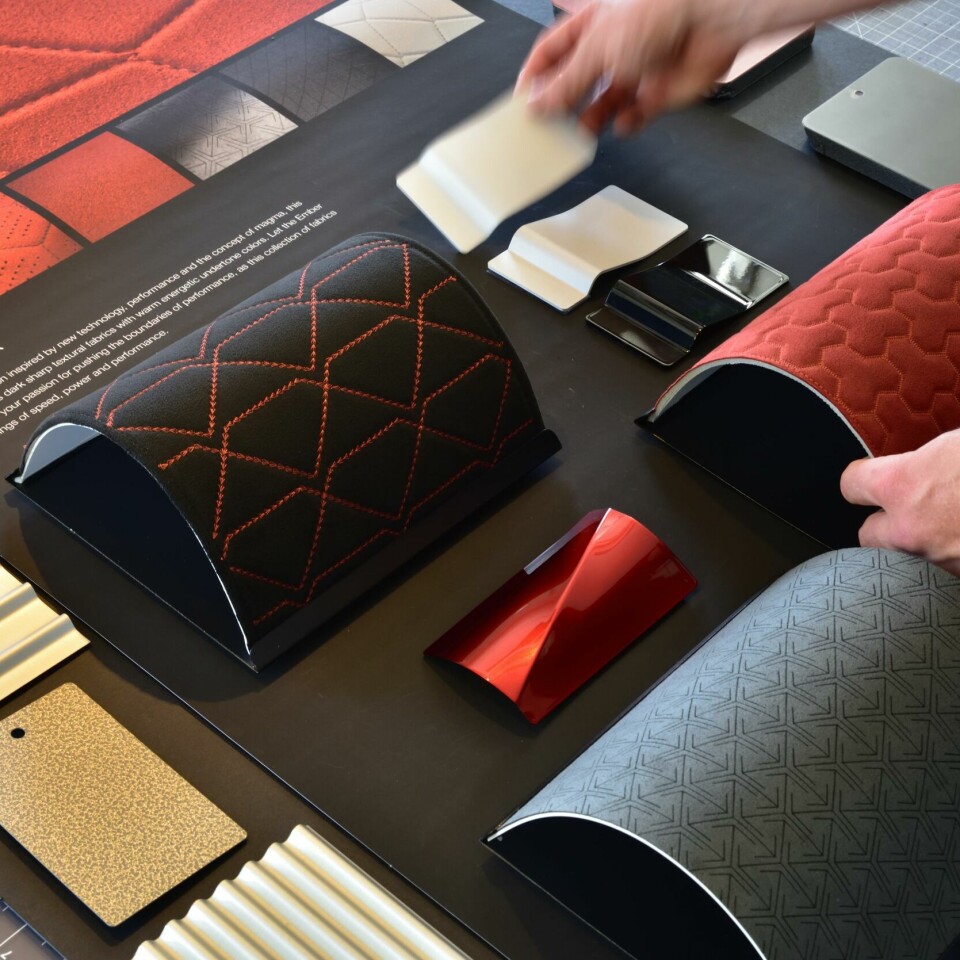
Shawmut is best known for its warp knit headliner, visor, and pillar fabric, as well as its fabric lamination technologies, where it has been a global market leader for decades.The company has seen an opportunity to bring its expertise elsewhere in the cabin and has employed a tried-and-trusted production technique that brings benefits in both the factory and the design studio.
“Neoluxe is a quality luxury suede material that has been engineered to solve two key industry problems,” says Dennis Hanuschik, president of Shawmut’s automotive division. “It addresses issues such as sustainability – Neoluxe uses 100% recycled PES yarns for a mono-material composite – and better processability at customer plants due to better technical parameters, such as elongation, and all with a better price-to-performance ratio.”
At its core, Neoluxe is an alternative to urethane-infused non-woven microfibre materials for automotive interior fabrics. It is lighter and can be made with up to 100% recycled PES content, and when combined with PES adhesives and substrates, creates an easily recyclable mono-material. A life cycle analysis (LCA) of the material has found it offers a significantly lower carbon footprint compared to its peers.
The material can be customised to the designer’s request within a very short period of time
Working on the next generation of automotive interiors will not be easy, with modular seating arrangements, heightened expectations for quality and ever-more scuptural surfacing across the cabin.
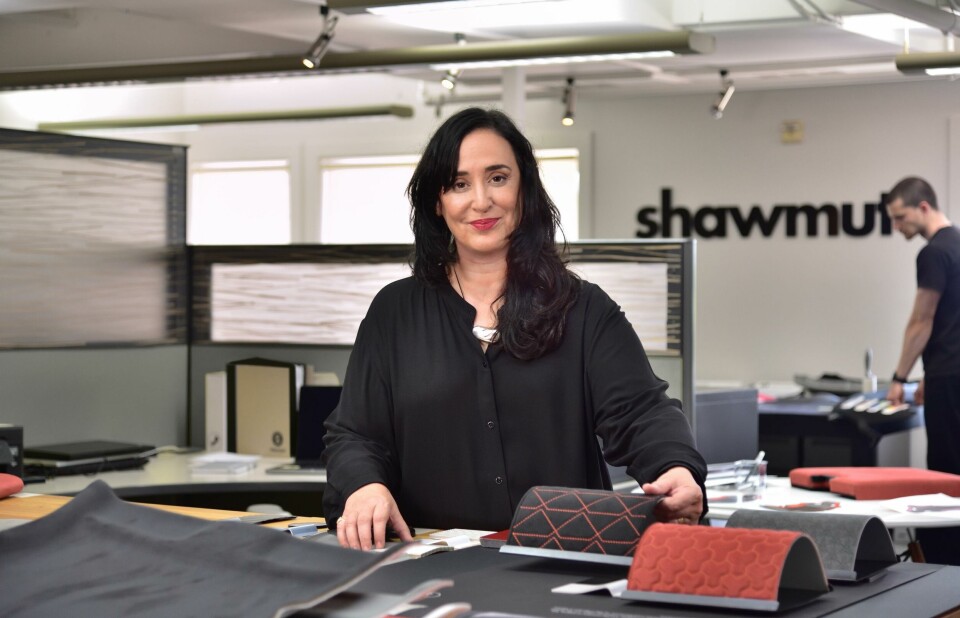
Indeed, Shawmut’s customers have highlighted the challenge of working with traditional non-woven suedes which are thicker and stiffer – not ideal when you are trying to wrap and trim complex surfaces. As a knitted material, Neoluxe does not suffer the same issue and still matches the high-end look and feel expected of a traditional suede. Crucially, it can be produced at high volumes at consistent quality to meet the needs of OEMs.
“Neoluxe is based on a well-known technology in warp knit fabric,” explains Mollie Engel, VP of design and development for Shawmut. “The beauty of this is the very consistent production capability, which allows designers to work with many added-value steps such as perforation, embossing, printing, laser, and other technologies.”
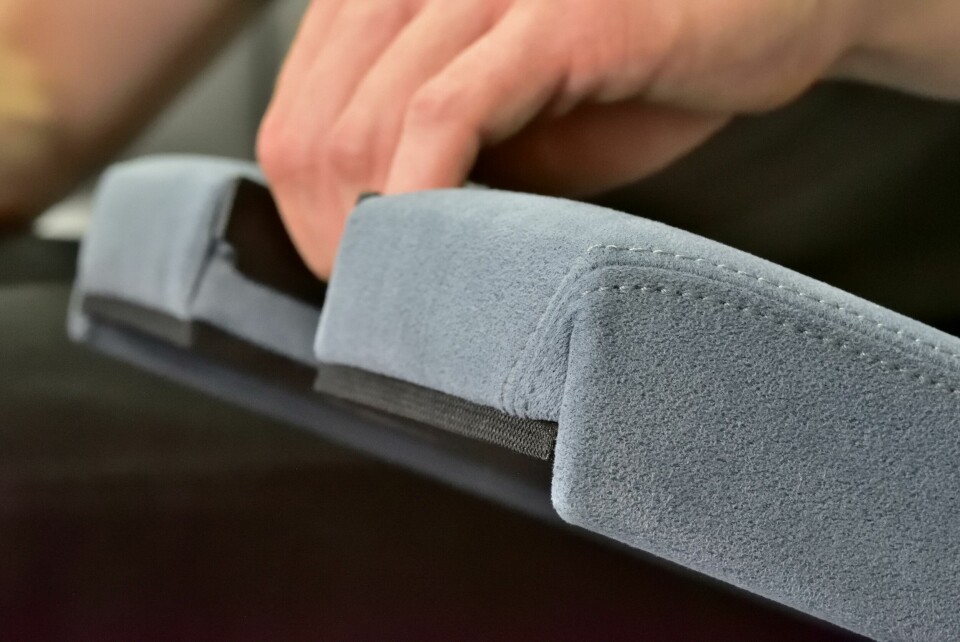
This workability will be of particular interest to design studios, which are under greater pressure than ever to iterate at speed and push the boundaries of creativity. Thankfully, Engel notes, “the material can be customised to the designer’s request within a very short period of time.”
Alongside Neoluxe is InfiniKnit, an innovative spacer knit alternative to traditional foam-based solutions and face fabrics. The dimensional knit structure features a plush inner layer that is seamlessly integrated into the face and back material. Another versatile alternative to what is already out there in the market, key applications include overhead systems, seats and doors as well as instrument panels and other interior trim.
Armed with both solutions, Shawmut believes its latest additions to the portfolio present a win-win, optimising the development process while tackling key industry concerns around sustainability.
“Our sustainability engineering team has been meeting with OEM designers to review LCA models,” concludes Hanuschik, “showing them the impact choices about fabric content, composite construction and even production location can have on LCA outcomes. It’s been eye-opening for them and made conversations about fabric design and selection far more engaging.”